Leading Engine Crankshaft Manufacturers: Quality and Innovation in Diesel Engine Parts
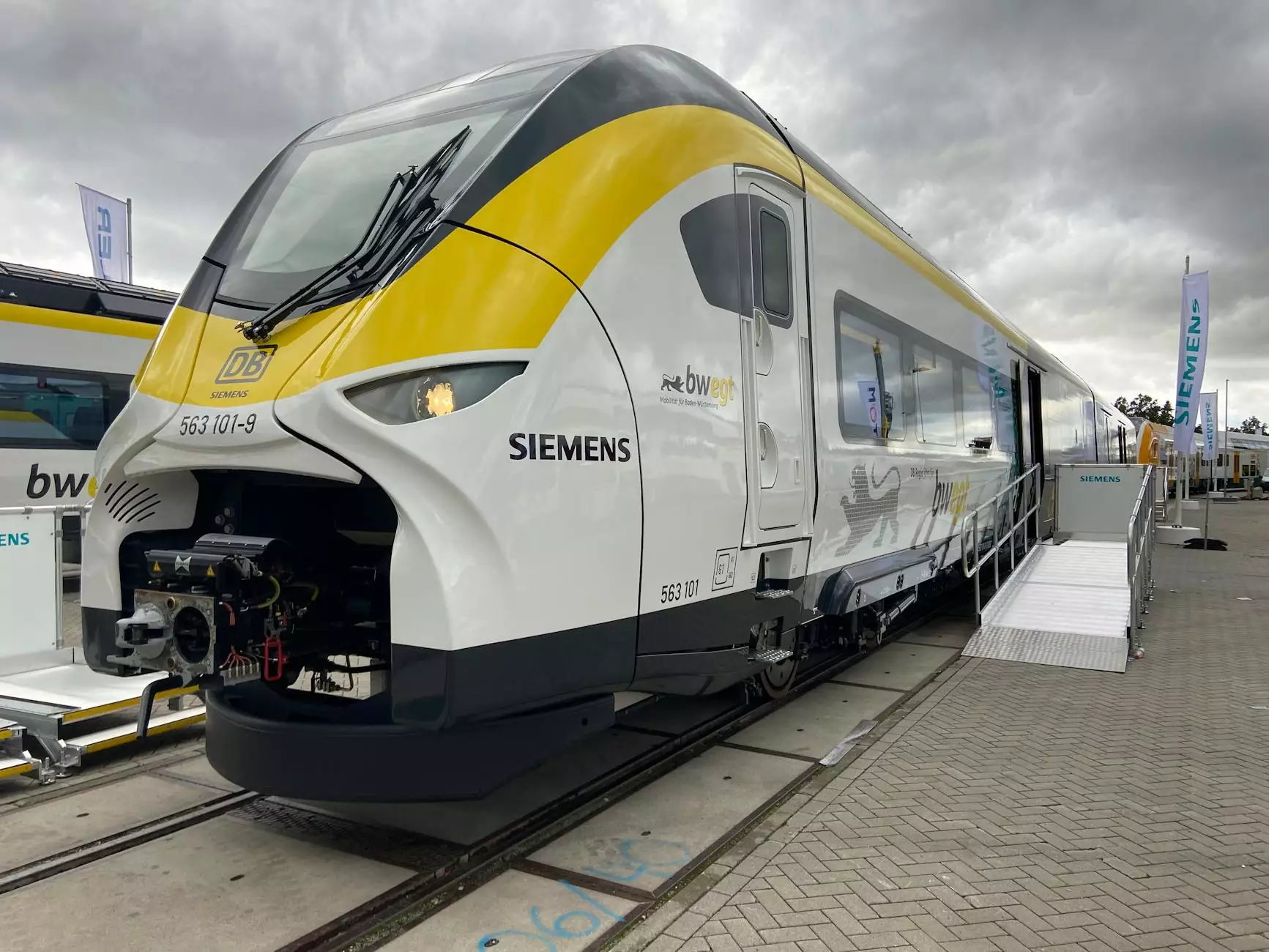
The world of engine crankshaft manufacturers has transformed significantly over the years. With a growing demand for high-quality diesel engines and their components, manufacturers are rising to the occasion to meet and exceed these market needs. This article delves deep into the intricate workings of the crankshaft—the heart of any internal combustion engine—and highlights the excellence provided by trusted manufacturers in the industry.
The Importance of Crankshafts in Diesel Engines
Crankshafts play a vital role in the operation of diesel engines. They serve multiple functions including:
- Converting linear motion into rotational motion: In diesel engines, the pistons move up and down within the cylinders, creating linear motion. The crankshaft converts this linear movement into rotational motion to power the vehicle.
- Balancing engine performance: A well-balanced crankshaft is crucial for smooth engine operation. It minimizes vibrations, which can lead to wear and tear on other engine components.
- Supporting multiple engine components: The crankshaft is the foundational element that connects to various components including the flywheel, pistons, and camshaft.
Why Choose Reputable Engine Crankshaft Manufacturers?
When it comes to engine crankshaft manufacturers, choosing a reputable supplier like client-diesel.com is essential. Here are some reasons why:
- Quality Assurance: Top manufacturers adhere to strict quality control measures, ensuring that every crankshaft meets the required specifications.
- Advanced Manufacturing Techniques: Utilizing the latest technological advancements, these manufacturers employ innovative techniques to enhance the durability and efficiency of their crankshafts.
- Customization Options: Leading manufacturers often provide custom solutions based on specific client requirements, allowing for tailored products that meet unique engine specifications.
- Expertise and Experience: With years of experience in the industry, these manufacturers possess invaluable knowledge that contributes to the superior design and engineering of their products.
Factors to Consider When Choosing Engine Crankshaft Manufacturers
Selecting the right manufacturer for engine crankshafts requires thorough consideration of several critical factors:
1. Reputation in the Industry
Conducting research into a manufacturer's reputation is crucial. Look for reviews and testimonials from other clients to gauge their satisfaction with the products and services provided.
2. Product Range
A diverse product range indicates a manufacturer's ability to cater to various engine types and specifications. This variability is essential, especially for businesses engaging in multiple engine types.
3. Technical Support
Reliable manufacturers offer ongoing technical support to assist clients with installation, maintenance, and troubleshooting of crankshafits.
4. After-Sales Service
The manufacturer’s reputation for customer service post-purchase can be a determining factor in maintaining a longstanding partnership. Excellent after-sales service can provide peace of mind regarding product reliability.
Insights into Top Engine Crankshaft Manufacturers
The following section explores some of the leading engine crankshaft manufacturers known for their excellence and commitment in the diesel engine parts sector.
Client Diesel: A Benchmark in Quality
Client Diesel stands at the forefront of the crankshaft manufacturing industry. With a commitment to providing cutting-edge solutions for diesel engines, this manufacturer excels in:
- Precision Engineering: Client Diesel utilizes state-of-the-art CNC machining technology to produce crankshafts that meet exacting specifications.
- Innovative Design: Their engineering team works diligently to create designs that enhance performance and longevity of engine components.
- Comprehensive Testing: Each crankshaft undergoes rigorous testing to ensure that it can withstand the harsh conditions of diesel engine operation.
XYZ Crankshaft Solutions
XYZ Crankshaft Solutions is another notable player in the industry, specializing in high-performance crankshafts tailored for heavy-duty applications. Known for:
- Robust Materials: They utilize high-grade steel alloys that provide exceptional strength and resistance to wear.
- Custom Fabrication: Their capability for custom fabrication allows them to meet specific client needs, catering to a diverse array of engines.
- Global Reach: With distribution networks across several regions, XYZ ensures timely supply and support for international clients.
Understanding the Manufacturing Process of Crankshafts
To appreciate the quality provided by leading engine crankshaft manufacturers, it's important to understand the intricate manufacturing process involved:
1. Material Selection
The journey begins with selecting the right material. Most crankshafts are made from forged carbon steel or cast iron, chosen for their strength and durability.
2. Forging or Casting
The material either undergoes a forging process, which involves shaping it under high pressure, or a casting process, where molten metal is poured into molds. Forged crankshafts typically offer better fatigue resistance.
3. Machining
Following the initial shaping, precision machining is carried out. This involves removing excess material using CNC machines to achieve the necessary tolerances.
4. Heat Treatment
Heat treatment processes such as quenching and tempering may be applied to enhance hardness and toughness, further increasing the longevity of the crankshaft.
5. Finishing
The final stage includes surface finishing processes such as grinding and polishing, which improve the surface characteristics and overall appearance of the crankshaft.
Technological Innovations Influencing Crankshaft Manufacturing
The manufacturing of crankshafts is continuously evolving, influenced by technological advancements. Here are some innovations making an impact:
- Computer-Aided Design (CAD): This technology allows for precise modeling and simulation of crankshaft designs, enabling manufacturers to assess performance before production.
- Advanced Materials: The introduction of lightweight materials such as titanium alloys is becoming popular, enhancing efficiency while reducing overall vehicle weight.
- 3D Printing: This revolutionary technology allows for rapid prototyping and production of complex crankshaft designs that were previously impossible to create with traditional manufacturing techniques.
The Future of Engine Crankshaft Manufacturing
The future of engine crankshaft manufacturers is bright, fueled by continuous innovation and an increasing demand for efficient, high-performance diesel engines. Some trends to look forward to include:
- Increased Automation: More manufacturers are incorporating automated processes to enhance precision and reduce production times.
- Sustainability Practices: Sustainable manufacturing practices, including recycling and reducing waste, are becoming a priority.
- Smart Manufacturing: The integration of IoT and AI in production processes is paving the way for smarter, more efficient manufacturing systems.
Conclusion
As demonstrated, the role of engine crankshaft manufacturers is crucial in the functioning of diesel engines. Committed manufacturers like Client Diesel exemplify excellence in quality, innovation, and customer satisfaction. By choosing the right manufacturer, businesses can ensure that they receive superior engine parts that enhance performance, reliability, and efficiency. The landscape of crankshaft manufacturing is poised for further advancements, and with it, the promise of a more sustainable and innovative future for diesel engines.