The Crucial Role of ABS Injection Molding Temperature in Business Success
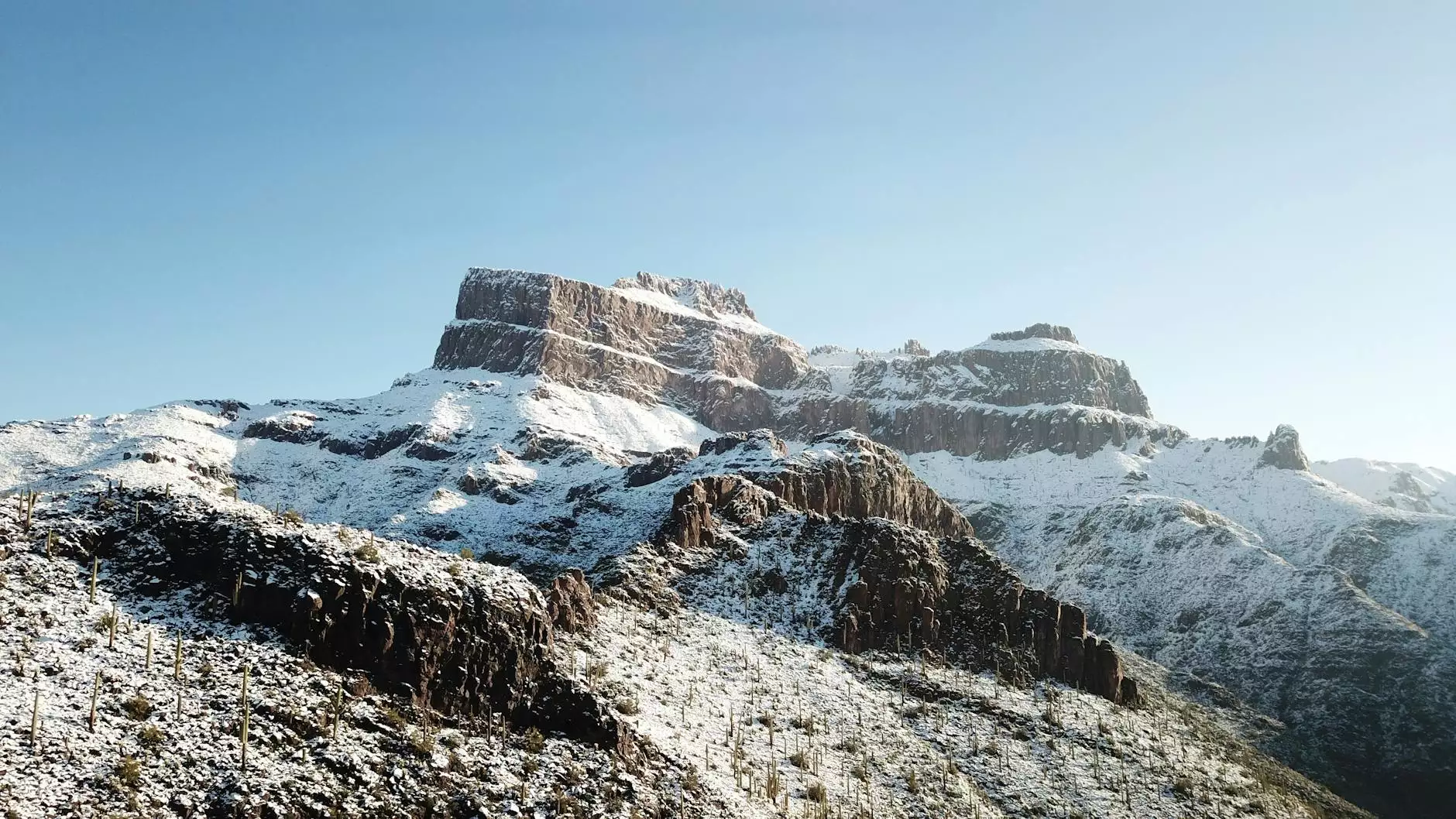
In the competitive realm of plastic manufacturing, understanding the nuances of ABS injection molding temperature is not merely a technical detail; it is a strategic advantage. The ability to manipulate these temperatures effectively can lead to enhanced product quality, reduced manufacturing costs, and increased output efficiency. This article delves deep into the intricacies of ABS injection molding, providing manufacturers with the knowledge necessary to optimize their processes and boost business performance.
What is ABS and Its Importance in Injection Molding?
ABS, or Acrylonitrile Butadiene Styrene, is a widely used thermoplastic polymer known for its strength and resilience. It features a combination of properties that make it an ideal choice for various applications, including:
- High impact resistance - Makes it durable for use in various products.
- Good thermal stability - Allows for higher processing temperatures.
- Excellent chemical resistance - Ensures longevity of the molded parts.
- Ease of processing - Facilitates quick and efficient production cycles.
Given these attributes, ABS is especially popular in the automotive, consumer goods, and electronic sectors, where precision and reliability are paramount. But to harness the full potential of ABS, manufacturers must grasp the significance of ABS injection molding temperature.
Understanding the Science Behind ABS Injection Molding Temperature
In injection molding, temperature is a critical parameter that affects every phase of the manufacturing process. From the melting of the polymer granules to the cooling of the final product, maintaining the right temperature is vital. Here’s how the ABS injection molding temperature influences each stage:
1. Melting Temperature
The initial stage of injection molding involves heating ABS pellets until they melt. The typical melting temperature for ABS is around 210°C to 250°C. Any fluctuations in this range can lead to:
- Inadequate melting - Results in poor flowability and inconsistency in the molded part.
- Overheating - Can degrade the polymer, leading to discoloration and loss of mechanical properties.
2. Injection Temperature
Once melted, the ABS must be injected into molds at optimal temperatures. This phase is crucial as it affects the filling of the mold. An ideal injection temperature for ABS should generally be between 230°C and 260°C. Too low a temperature can cause:
- Poor mold filling - Leading to incomplete parts.
- Short shots - Where the polymer does not fill the entire mold cavity.
Conversely, excessively high injection temperatures may cause:
- Burning of the material - Leading to surface defects.
- Increased cycle times - Due to the need for longer cooling periods to solidify the part.
3. Cooling Temperature
After the injection, the molded part must cool down to solidify. The cooling temperature can greatly influence the dimensional accuracy and surface finish of the final product. Factors to consider include:
- Cooling rate - A faster cooling rate can lead to warping, while a slower rate may increase cycle time.
- Mold temperature - Optimal mold temperatures usually range from 20°C to 60°C depending on the part size and complexity.
Best Practices for Managing ABS Injection Molding Temperature
To achieve optimal results with ABS injection molding, manufacturers should implement the following best practices:
Use Advanced Temperature Control Systems
Investing in high-quality temperature control systems can ensure that both the injection barrels and molds maintain the desired temperatures throughout the production cycle. This minimizes variations and enhances the consistency of the molded products.
Regular Calibration of Equipment
Periodic calibration of all equipment involved in the injection molding process is essential. This includes verifying that temperature sensors are functioning correctly and that heating elements are effective in maintaining the required temperature ranges.
Conducting Regular Process Monitoring
Implementing a continuous monitoring system can help detect any deviations from the set temperature parameters in real-time. This proactive approach allows for immediate adjustments, preventing potential defects.
Employee Training and Awareness
Ensuring that all staff are adequately trained in understanding the importance of ABS injection molding temperature will foster a culture of quality and attention to detail on the shop floor.
Benefits of Optimizing ABS Injection Molding Temperature
By focusing on optimizing injection molding temperature for ABS, businesses can reap numerous benefits which include:
- Improved Product Quality - Consistent temperature control leads to high-quality finished products with better surface finishes and dimensional accuracy.
- Increased Production Efficiency - By reducing cycle times and defective product rates, manufacturers can boost production output significantly.
- Cost Reduction - Minimizing scrap rates and rework needs contributes to lower manufacturing costs and higher profitability.
- Enhanced Sustainability - Efficient temperature management reduces energy consumption, contributing to more sustainable manufacturing practices.
Conclusion: The Strategic Advantage of ABS Injection Molding Temperature Management
In conclusion, mastering the intricacies of ABS injection molding temperature is essential for companies in the plastic manufacturing sector. The impact of temperature on the quality, efficiency, and cost-effectiveness of production processes cannot be overstated. By implementing best practices, leveraging advanced technology, and fostering a culture of continuous improvement, businesses like hanking-mould.com can not only meet but exceed industry standards. This dedication to quality and efficiency will serve as a catalyst for sustainable growth and superior customer satisfaction, ensuring a competitive edge in today’s dynamic market.