The Ultimate Guide to Auto Parts Mold
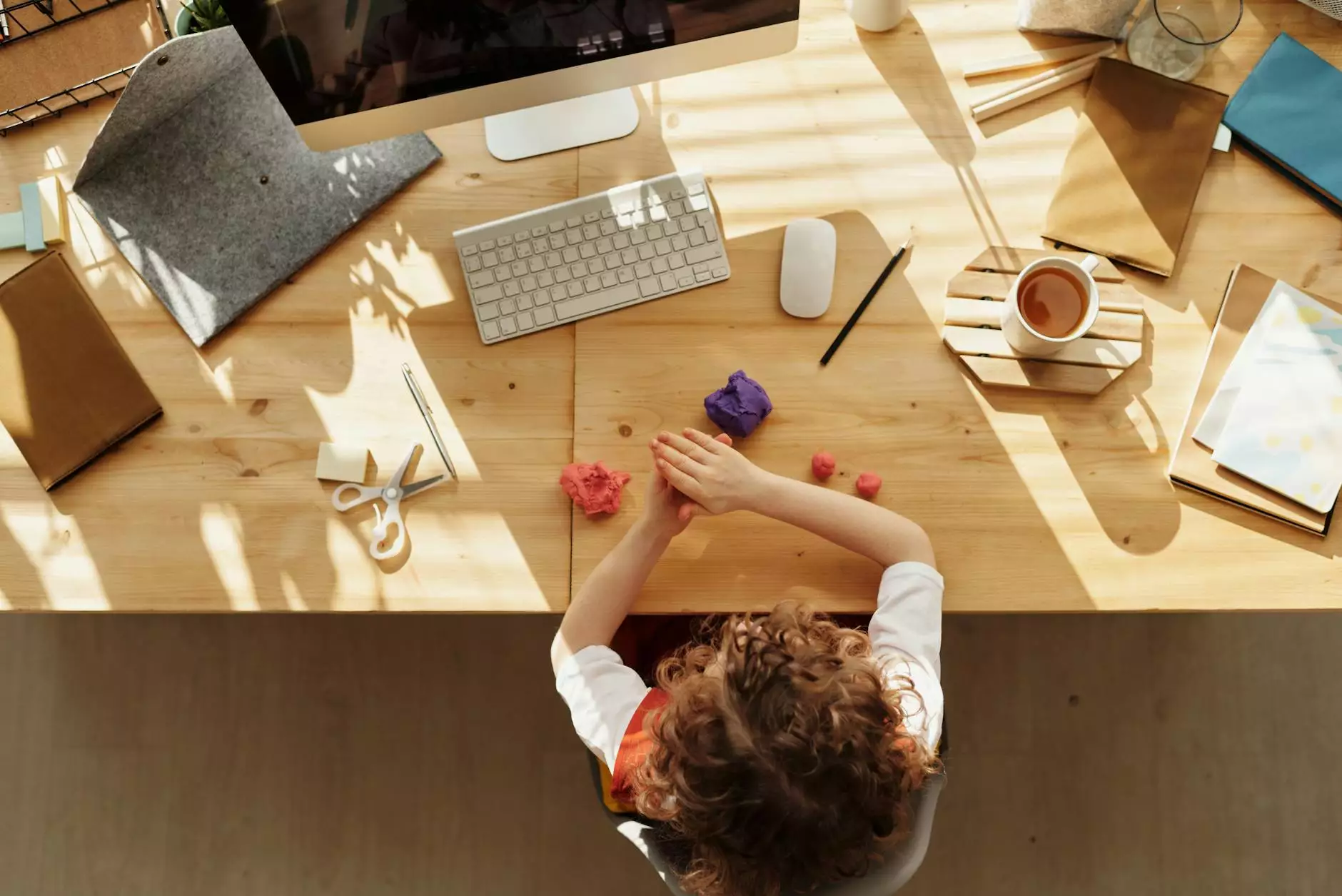
The automotive industry has witnessed a remarkable transformation over the past few decades. Among the various components that contribute to this evolution, auto parts mold plays a crucial role. This article delves deep into the realm of auto parts molds, exploring their significance, the manufacturing processes involved, and the impact they have on the automotive industry. Whether you are a manufacturer, a supplier, or just an enthusiast, understanding the intricacies of auto parts mold can provide invaluable insights.
Understanding Auto Parts Mold
The term auto parts mold refers to the specialized molds used to produce components for automobiles. These molds are pivotal in ensuring that the parts are manufactured to precise specifications, allowing for better performance, safety, and aesthetics. The process of creating these molds is an intricate blend of art and science, requiring significant expertise and advanced techniques.
The Importance of Molds in Automotive Manufacturing
In the automotive sector, every detail counts. Auto parts molds enable manufacturers to produce complex shapes and structures that are otherwise impossible to achieve through traditional manufacturing methods. Here are some key reasons why auto parts molds are essential:
- Precision: Molds ensure that each part is produced with exact specifications, which is critical for assembly.
- Durability: High-quality molds lead to durable parts that withstand the rigors of road use.
- Efficiency: The molding process is highly efficient, allowing for mass production without compromising quality.
- Cost-effectiveness: While the initial investment in molds can be significant, they reduce labor and material costs in the long run.
The Process of Creating Auto Parts Molds
Creating a high-quality auto parts mold involves several meticulous steps, each crucial to ensuring the final product meets industry standards. This process can be broken down into the following stages:
1. Design and Engineering
The first stage in creating an auto parts mold is the design phase. Skilled engineers use advanced computer-aided design (CAD) software to create detailed models of the parts to be produced. This stage requires a thorough understanding of both the product specifications and the manufacturing processes involved.
2. Material Selection
Once the design is finalized, the next step is selecting the appropriate materials for the mold. Common materials include:
- Steel: Known for its durability and strength, steel is the most popular choice for high-volume production.
- Aluminum: Lightweight and excellent for lower-volume production, aluminum molds heat up quickly, reducing cycle times.
- Composite Materials: Offer a balance between weight and strength, often used for specialty applications.
3. Machining the Mold
After selecting the materials, the next stage is machining. This involves cutting, drilling, and shaping the material into the desired mold form. High-precision CNC (Computer Numerical Control) machines are often used to ensure the highest levels of accuracy.
4. Mold Assembly
Once the individual pieces have been machined, they are assembled into a complete mold. This stage involves fitting the cooling and heating channels, which are crucial for maintaining optimal temperatures during the injection process.
5. Testing and Quality Control
Before the mold is put into production, it undergoes rigorous testing to ensure it meets all specifications. This step is critical for identifying any potential issues that could impact the quality of the auto parts produced.
Types of Auto Parts Mold
Several types of molds are utilized in the production of auto parts, each suited for different applications. Here are some of the most commonly used types in the industry:
1. Injection Molds
Injection molds are perhaps the most widely used in the automotive industry. This process involves injecting molten plastic into the mold cavity to create the desired shape. Injection molds are known for their efficiency and ability to produce high volumes of parts quickly.
2. Blow Molds
Blow molds are used for manufacturing hollow plastic parts, such as fuel tanks and air ducts. The process involves inflating a heated plastic tube until it conforms to the shape of the mold.
3. Compression Molds
Compression molding is another method used to create auto parts molds, particularly for rubber and composite materials. This technique involves placing a pre-measured amount of material into an open mold cavity and applying heat and pressure to shape it.
Benefits of Using High-Quality Auto Parts Molds
Investing in high-quality auto parts molds provides numerous advantages for manufacturers:
- Enhanced Performance: Quality molds ensure that the parts produced meet the stringent performance standards required in the automotive industry.
- Improved Safety: Well-manufactured auto parts reduce the risk of failures and accidents on the road.
- Increased Production Speed: Efficient molds can significantly reduce production times, allowing manufacturers to meet market demands more agilely.
- Longer Lifespan of Parts: Investing in quality molds results in parts that are more durable and longer-lasting.
The Role of Hanking Mould in Auto Parts Mold Production
At Hanking Mould, we specialize in the design and manufacture of high-quality auto parts molds that cater to the unique needs of the automotive industry. With years of experience and expertise in the field, we are dedicated to delivering innovative solutions that enhance the efficiency and effectiveness of automotive component production.
Why Choose Hanking Mould?
Choosing the right mold maker is crucial for your production process. Here are several reasons why Hanking Mould stands out:
- Expert Team: Our team of experienced engineers and designers leverage the latest technology to create state-of-the-art molds.
- Customer-Centric Approach: We prioritize our clients' needs, providing tailored solutions that ensure satisfaction.
- Quality Assurance: Every mold undergoes rigorous testing to guarantee it meets industry standards.
- Innovation: We are committed to continuous improvement and innovation in mold design and manufacturing processes.
Future Trends in Auto Parts Mold Manufacturing
The automotive industry is evolving rapidly, and so are the trends in auto parts molds. Some anticipated trends include:
1. Sustainable Materials
With the increasing focus on sustainability, there is a growing demand for molds that can produce parts using eco-friendly materials. Manufacturers are exploring bioplastics and recyclable materials to produce more sustainable auto components.
2. Advanced Technology Integration
Technologies such as 3D printing are gaining traction in mold production. This enables rapid prototyping and more complex mold designs, further enhancing customization capabilities.
3. Automation and Smart Manufacturing
The rise of Industry 4.0 is transforming the automotive manufacturing landscape. Automated systems and smart technologies will play a crucial role in making the mold manufacturing process more efficient, reducing lead times and costs.
Conclusion
In conclusion, the importance of auto parts molds in the automotive industry cannot be overstated. With their critical role in ensuring precision, durability, and efficiency in manufacturing, investing in high-quality molds is essential for any automotive manufacturer. At Hanking Mould, we are committed to pushing the boundaries of mold technology and providing our clients with the best possible solutions for their manufacturing needs.
For more information about our services in plastic mold making and plastic injection mold manufacturing, visit our website at hanking-mould.com or contact us today.