Understanding Injected Molded Plastic and Its Business Applications
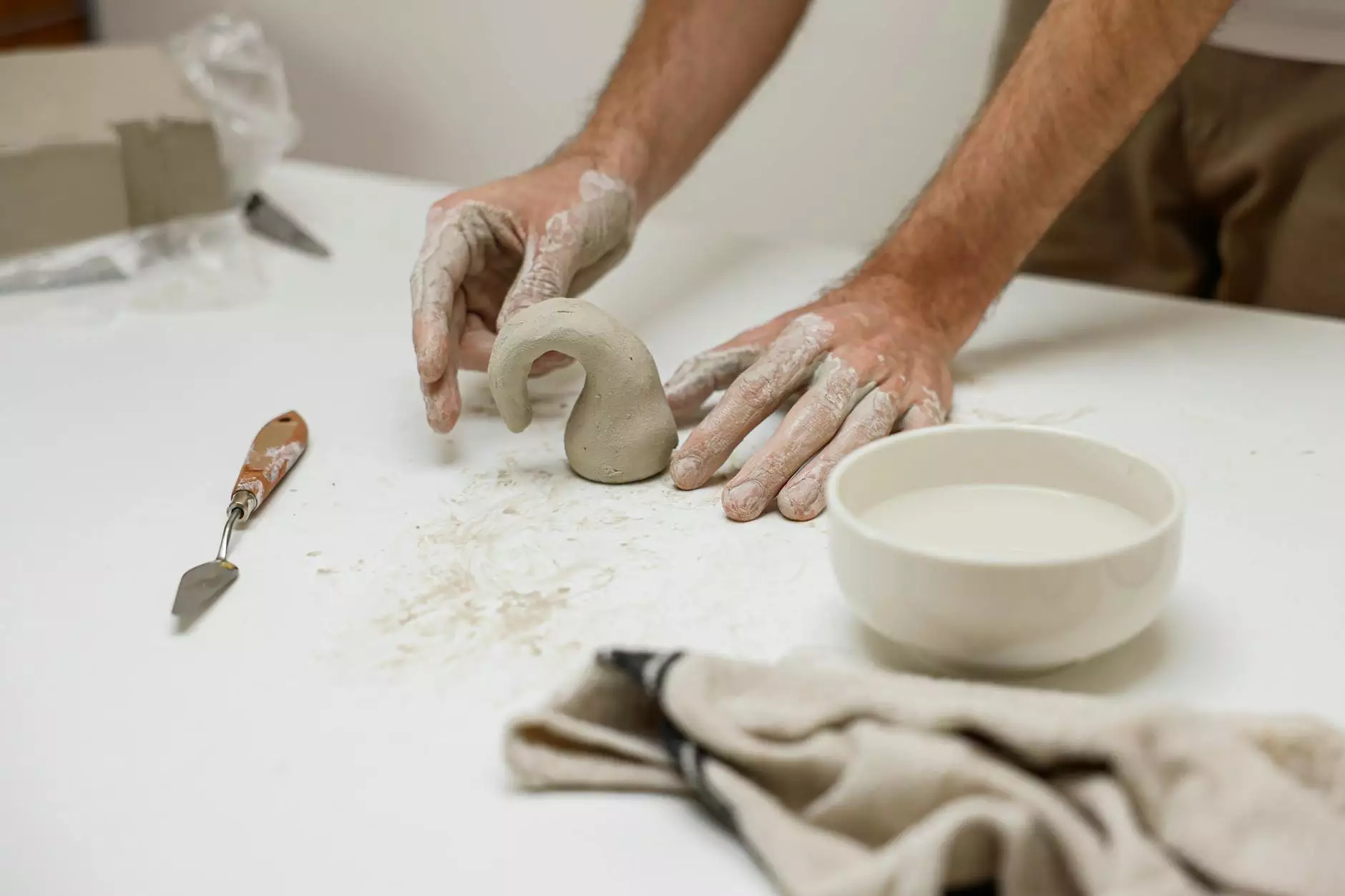
The manufacturing industry has seen immense transformations over the years, particularly with the advent of technologies that allow for more efficient production methods. One such method that has gained significant traction is injected molded plastic, a process that has revolutionized the way various products are created. This article delves deep into the fascinating world of injected molded plastic, the business implications, and how it integrates with metal fabricators to bolster efficiency and quality in manufacturing.
What is Injected Molded Plastic?
Injected molded plastic is a manufacturing process for producing parts by injecting molten material into a mold. This method is widely used in the plastic manufacturing industry due to its ability to create complex shapes accurately and consistently. It involves the following primary steps:
- Material Preparation: The process begins with thermoplastic or thermosetting polymers being fed into a heated barrel where they are melted.
- Injection: The molten plastic is then injected into a mold under high pressure.
- Cooling: Once the mold is filled, the material cools, solidifying into the desired shape.
- Mold Removal: Finally, the mold opens, and the part is ejected.
The Advantages of Injected Molded Plastic
There are numerous reasons why businesses choose injected molded plastic as their preferred manufacturing method:
- Cost-Effectiveness: Once the initial mold is made, the cost per part is significantly lower, especially for large production runs.
- Precision: This process allows for tight tolerances and high-quality finishes, making it ideal for intricate designs.
- Material Versatility: A wide variety of materials can be used, including elastomers, nylon, and other robust thermoplastics.
- Speed: The rapid cycle times mean that mass production can occur quickly, reducing lead times and fulfilling market demands efficiently.
Applications of Injected Molded Plastic in Business
Injected molded plastic finds application across numerous industries. Here are a few prominent sectors that benefit significantly from this technology:
1. Automotive Industry
The automotive sector is one of the largest consumers of injected molded plastic parts. From dashboard components to housings for electronic devices, the use of plastic significantly reduces vehicle weight, improving fuel efficiency while also providing design flexibility.
2. Consumer Electronics
Consumer electronics manufacturers frequently rely on injected molded plastic for creating durable and aesthetically appealing casings, connectors, and various internal components, thus enhancing functionality and user experience.
3. Healthcare Products
With an increasing demand for affordable and reliable medical devices, the healthcare industry utilizes injected molded plastic for items like syringes, IV bags, and other instruments requiring precision and hygiene.
4. Packaging Solutions
In the packaging sector, injected molded plastic offers flexibility and innovation with custom designs, ensuring product safety and longer shelf lives.
Metal Fabricators and Their Role in the Injected Molded Plastic Industry
While injected molded plastic primarily revolves around plastic manufacturing, metal fabricators play an instrumental role in this ecosystem:
Integration of Metal and Plastic
In many applications, it's common to find metal and plastic components working together. Metal fabricators provide precision-engineered metal parts that complement injected molded plastic components, creating hybrid products that leverage the strengths of both materials. For instance:
- Durability: Hybrid components combine the strength of metal with the lightweight nature of plastic.
- Cost Efficiency: Using plastic where possible reduces manufacturing costs while maintaining performance.
- Versatility: This integration allows for innovative designs that increase functionality.
Tooling and Mold Creation
The creation of molds is a critical aspect of the injected molding process, and this is where metal fabricators shine:
- Precision Manufacturing: Metal fabricators create high-quality molds that ensure precision in the manufacturing process.
- Durability: Metal molds offer high durability which allows for extensive use before needing replacement.
- Customization: Tailored molds can be designed to suit specific needs, resulting in unique end products.
Challenges in the Injected Molded Plastic Industry
Despite its numerous benefits, the injected molded plastic industry also faces challenges that businesses need to navigate:
1. Environmental Concerns
Plastic waste continues to be a significant environmental issue. Companies are under increasing pressure to implement sustainable practices, including recycling and the use of biodegradable materials.
2. Production Costs
While the cost per unit is low for large quantities, the initial investment in molds can be high. Businesses need to carefully consider the economic viability of projects based on their production scale.
3. Market Competition
The rise of advanced manufacturing technologies means that companies specializing in injected molded plastic must continuously innovate to maintain a competitive edge. Failure to do so can lead to a loss of market share.
The Future of Injected Molded Plastic
The future looks promising for the injected molded plastic industry, driven by technological advancements and evolving market demands:
1. Advancements in Materials
Innovations in plastic materials, such as the development of lightweight composites and stronger polymers, will enhance the application of injected molded plastic across various sectors.
2. Automation and Smart Manufacturing
The implementation of automation and Industry 4.0 concepts will streamline production processes further, minimizing waste and maximizing efficiency, thereby fostering sustainable growth.
3. Focus on Sustainability
As ecological awareness rises, manufacturers will increasingly turn to sustainable practices, including recycling initiatives and the use of more environmentally friendly materials.
Conclusion
The remarkable journey of injected molded plastic reflects the dynamic nature of the manufacturing industry. Its efficiency, cost-effectiveness, and adaptability make it a cornerstone for countless applications spanning diverse sectors. As businesses strive to keep pace with technological advancements and sustainability goals, the integration of solutions from metal fabricators alongside injected molded plastic technology will undoubtedly play a pivotal role in shaping the future of manufacturing.
For businesses looking to leverage the benefits of injected molded plastic, partnering with experienced metal fabricators can offer a significant competitive advantage. Together, they can enhance product functionality, innovate designs, and deliver high-quality outcomes that meet the demands of today's fast-paced market.