Understanding Injection Plastics in the Metal Fabrication Industry
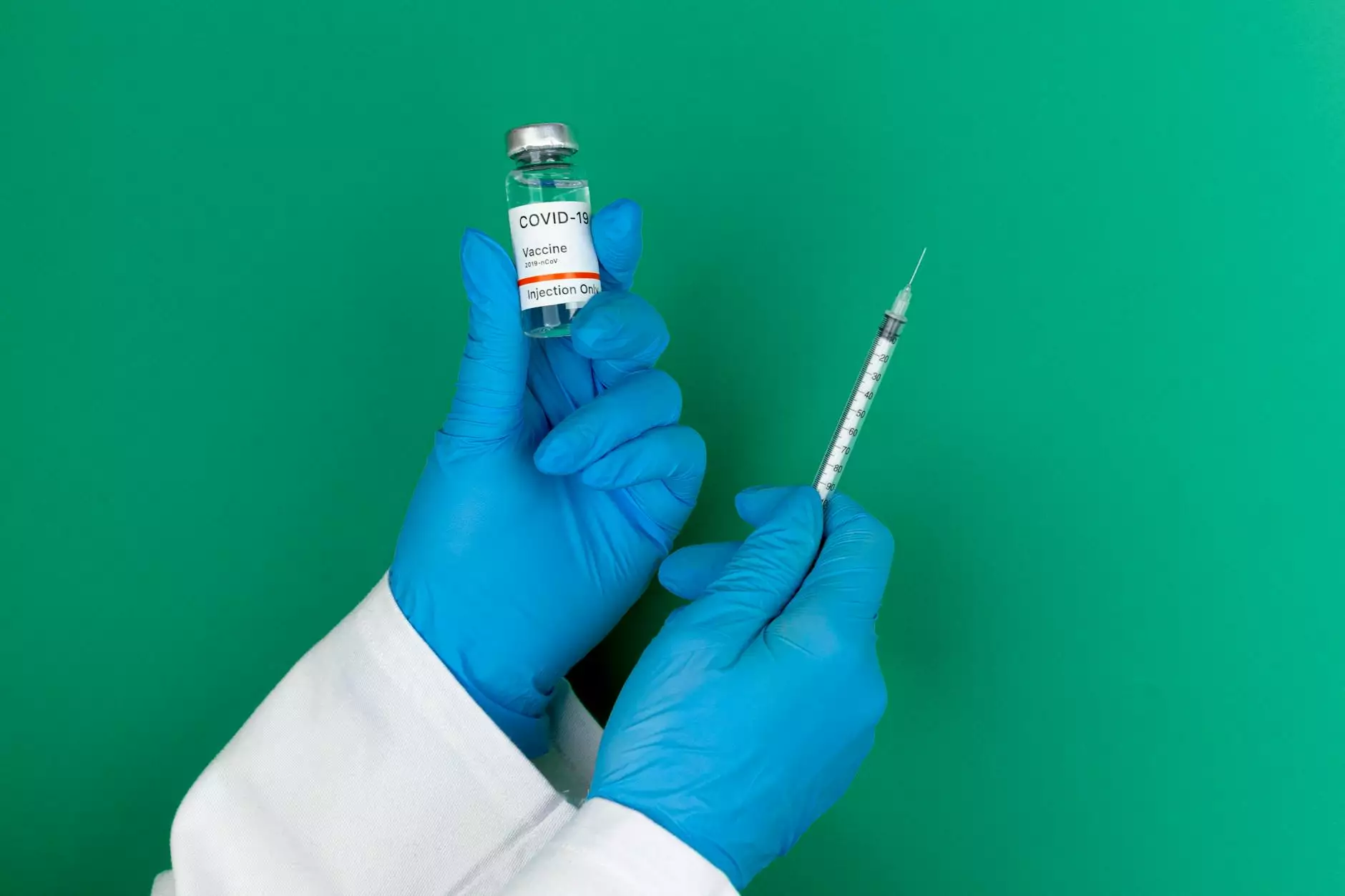
The world of injection plastics has transformed the landscape of manufacturing, especially within the realm of metal fabricators. This revolutionary technique not only enhances product quality but also optimizes processes and reduces costs. In this article, we delve deep into the mechanisms of injection plastics, their applications, advantages, and why they are crucial for the future of manufacturing.
What are Injection Plastics?
Injection plastics refer to the process of creating plastic products by injecting molten plastic into a mold. This method allows for the mass production of complex shapes with high precision. Through a detailed understanding of this process, manufacturers can harness its benefits to improve their product offerings. The molding process can use various types of thermoplastic and thermosetting materials, enabling a diverse range of applications.
The Injection Molding Process
The injection molding process encompasses several key steps, each integral to creating high-quality plastic components:
- Material Preparation: The plastic material, often in the form of pellets, is carefully dried and prepared to ensure optimal flow during injection.
- Heating: The pellets are heated in a barrel until they reach a molten state, allowing for easy injection into the mold.
- Injection: The molten plastic is then injected into a pre-designed mold under high pressure, filling the cavity to create the desired shape.
- Cooling: After injection, the mold is cooled to solidify the plastic, ensuring it retains the precise shape and dimensions of the mold.
- Demolding: Once cooled, the mold opens, and the finished product is ejected. This step often includes trimming away excess plastic, known as flash.
Applications of Injection Plastics in Metal Fabrication
In the field of metal fabrication, injection plastics serve numerous functions, enhancing both metal parts and the manufacturing process itself:
- Component Encasements: Injection-molded plastics can serve as protective encasements for metal components, providing insulation and shielding from environmental factors.
- Integrated Assemblies: Plastic parts can be incorporated into metal assemblies to create multifunctional components that reduce the need for additional fasteners.
- Prototyping: Manufacturers utilize injection plastics for rapid prototyping, allowing them to create visual and functional models before committing to metal fabrication.
- Finishes and Coatings: Injection plastics can also act as a finish for metal parts, offering an aesthetic appeal while protecting against corrosion.
Advantages of Using Injection Plastics
The integration of injection plastics into metal fabrication comes with a plethora of benefits that elevate productivity and quality:
1. Cost-Effectiveness
By streamlining production processes, injection molding reduces labor and material costs. The efficiency of creating multiple parts simultaneously makes it financially viable for large-scale productions.
2. Versatility
Injection plastics can be molded into virtually any shape, allowing for creative and functional designs that may not be achievable with traditional metal fabrication techniques.
3. Precision and Consistency
Injection molding produces high-precision parts with consistent dimensions, reducing the need for extensive post-production adjustments. This quality assurance is vital in maintaining industry standards.
4. Reduced Manufacturing Time
The speed of the injection molding process enables quicker turnaround times from design to production, a critical factor in today’s fast-paced market.
Challenges in Injection Molding
Despite its numerous advantages, the injection molding process is not without challenges. Understanding these can help manufacturers like those at deepmould.net navigate potential pitfalls:
- Initial Setup Costs: The cost of creating molds can be high, particularly for complex designs; however, the investment pays off over time with mass production.
- Material Limitations: Not all plastics are suitable for injection molding, and the choice of material can affect the final product's performance.
- Environmental Impact: The production of plastics raises concerns regarding sustainability; thus, manufacturers are encouraged to explore biodegradable options.
Future Trends in Injection Plastics
As technology advances, the world of injection plastics continues to evolve. Some emerging trends include:
1. Sustainable Practices
The push for sustainability is leading manufacturers to seek eco-friendly materials and processes. Bioplastics and recycled materials are gaining traction in the injection molding industry.
2. Advanced Technologies
3D printing and automation are revolutionizing the injection molding process, offering greater efficiency and customization capabilities that were previously unimaginable.
3. Industry 4.0 Integration
The incorporation of IoT (Internet of Things) technologies into manufacturing processes provides real-time data collection and analysis, enhancing decision-making and efficiency.
Conclusion: The Importance of Injection Plastics in Metal Fabrication
The role of injection plastics in the metal fabrication industry cannot be overstated. As manufacturers seek innovative ways to enhance their products and processes, understanding and leveraging the benefits of injection molding will be crucial. The future lies in integrating advanced techniques, materials, and sustainable practices that not only boost productivity but also fulfill the growing demand for environmentally responsible manufacturing.
Deepmould.net is at the forefront of these advancements in the injection plastics sector, providing valuable insights and high-quality products that cater to the evolving needs of metal fabricators. By harnessing the power of injection plastics, businesses can pave their way to success in an increasingly competitive landscape.